Our storeroom and spare parts organization are usually the area with more opportunities regarding reliability operation.
What does good look like? What elements are needed? How can we change our stores towards these best practices?
Several elements are taken in consideration:
- Master Data
- Storeroom Organization
- Storeroom Operation
- Inventory Control
- Quality Program
- PM program
- Reports, KPI’s and Data analysis
- Inventory Optimization
Spare parts can be defined as a duplicate or interchangeable part used for the repair or replacement of failed or worn parts.
Additionally, we can say that the parts function is to sit on a shelf, or have it easily accessible, so it is available when needed.
First, we are going to look at Master data and what is needed for best practices
Master data – We look at what information is available.
This includes:
1) Meaningful description:
We recommend the following naming convention: Noun, modifier 1, modifier 2… The limits are usually the size of the CMMS field that holds the description.
During a recent assignment, I was working with a CMMS where the parts description had 255 characters! This was a dream. We were able to populate the description with meaningful information, all that we wanted.
The goal of any part description is to be able to identify a needed part in the system or report, WITHOUT going to additional screens.
2) Manufacturer & manufacturer part number
– The best practice is to have the correct information. These two fields are extremely important when restocking based on inventory levels. What is the correct information? It is when you can purchase the part in an open market without problems or looking for additional information. This information is usually stamped on the part or identified in the box or original packaging.
The parts and the equipment manufacturer are not the same. Sometimes the equipment manufacturer places his part identification number in exploded views, manuals and part list. When this happens, we end up with an incorrect part manufacturer and part number, buying it from an equipment manufacturer and paying more for it. It is fair to mention that sometimes equipment manufacturers will have typical parts modified (base, mounting, etc.). This is not common but happens.
3) Specifications
Includes tolerances, materials, hardness, length, etc. This is particularly important in regulated industries where the term “Like for Like” is predominant. This is a key element when considering a parts quality program; we’ll talk about this in more detail.
4) Primary vendor and vendor part number
This is usually who I’d buy this item from. Parts specifications are needed especially when challenged from purchasing regarding a selected vendor. If a vendor can provide the part WITH the same specifications at a lower cost, well, let’s buy it from him.
Storeroom Organization
Storerooms need to be organized in such a way that anybody can find any part. This involves two major areas: physical location and a means to find a part.
Physical organization
This is the physical location of the part. It can be in one or several locations. A best practice regarding location is to identify the part in its most precise location.
Examples:
Cabinet# – Drawer# – row – pocket
This can be accomplished when loading or maintaining a drawer. Always start on the left of the drawer and add rows and pockets as you add parts.
Always leave the equivalent of 2 rows to compensate for the overflow of parts in any particular moment. If by any chance you receive additional part that cannot be placed in the original location, such as for a shutdown, you can place them in another section of the storeroom that can be called “overflow”.
Most CMMS can deal with multiple locations.
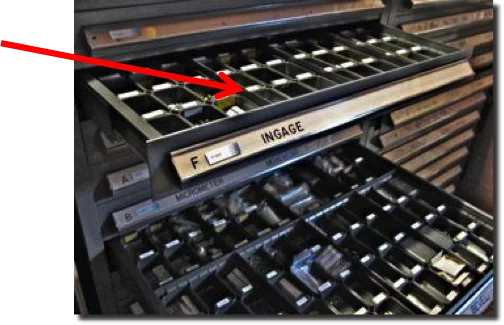
Row# – Rack# – shelf – position
A position on the shelf can be done by using plastic containers or boxes. This will give a unique position for the part on the shelf. In addition, you can use one location for multiple parts if needed.
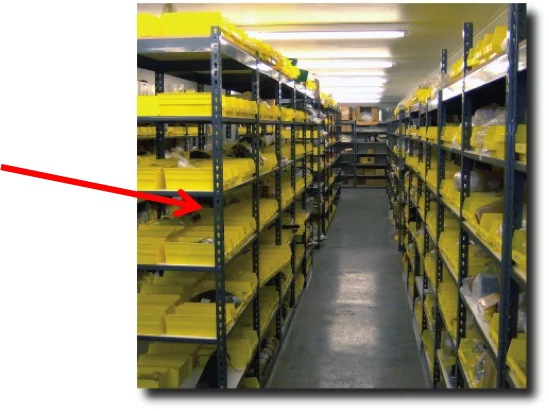
Another method of getting that unique position is by placing colored tape marking the position.
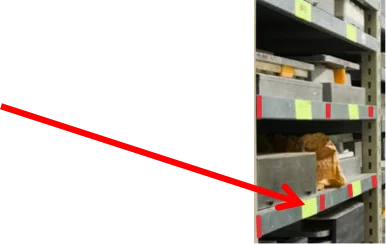
What and where to locate a part
Locating a spare in storeroom has always been a challenge. We ask questions such as “This bearing, should I place it with the general bearing commodity or should I place it with the specific equipment it is used on?”
There are no specific answers, but there are guidelines that will help you make the decision. Most Inventory systems can handle multiple part locations.
That means that you can have 10 bearings in location XX and 5 of the same bearings in location YY. This functionality is solid; however, there are a few precautions you should take:
- Everyone needs to know that they are multiple locations; a common situation is a line mechanic not finding a bearing in YY location (chaos breaks out) and not knowing it has another location.
- Inventory controls needs to be in place (IRA counts, max / min levels)
- Inventory re-order system needs to be challenge and verify that it takes into account both locations
Some parts location options:
All commodities together
Placing together all bearings, fuses, electrical parts, mechanical seals, etc.
Some Advantages:
- Locating similar parts (like for like) when adding a new part into the system.
- Control of inventory levels.
- Inventory value $$ can be improved
Some Disadvantages
- Equipment Spare Parts list or BOM’s needs to be accurate and truthful.
- Inventory levels needs to account for parts issues on all equipment
Parts stored by equipment
placing together all compressor part, pumps, winder, etc.
Some Advantages:
- Negligible need for accurate Equipment spare part list
- Easy to find, everything is in the same rack, drawer, etc.
Some Disadvantages:
- Good possibility of duplicated parts
- Inventory value $$ increases
- If part not on stock, difficult to find another one.
Finding a part
As mentioned above, the ease of finding a part in any inventory depends on various factors such as:
- Where and how was it stored (see item #2 above)?
- Did I find it on a previous occasion?
- Do I know how to find a part in the CMMS?
- Do I know how my storeroom is organized
This is a true story in which I was involved. By nature people are resistant to change.
When the change is in a part location, it is not resistance, it is a rebellion!! “If I have been finding this sprocket for the last 15 years in this location, why change it?”
This is what I recently heard in a plant. The scenario was that the plant purchased two vertical storage units in order to provide more space for a plant expansion.
The storeroom was impacted and needed to give up floor space.
The solution: Vertical Storage Units!
Yes indeed, the logic and studies told management that this was the correct movement.
What happen after the implementation?
Trades productivity went down & machine downtime went up. Why? The trades were not able to find parts, especially in the 2nd and 3rd shifts, when no storeroom personnel were available.
Before the Vertical units, rows of racks and open shelving were the storage method. They were organized by equipment; however a formal spare parts list did not exist.
When somebody wanted to find a part, they stood in front of the rack and more or less knew where it was. After that, pulling and opening boxes was involved.
The crazy thing was they did it very fast (used it before or somebody did).
When parts were moved to the vertical storage, a cross reference of parts was created (old location vs new location).
However, in order to be more efficient in the storage, they moved to storage by commodity method.
Not only the parts were moved, but they organized it differently!!
Like I mentioned, it was chaos.
After a few weeks, processes were established and people were trained.
The plant started to build Spare Part list by equipment and printouts were available (hardcopy and electronic).
Posters on “How to search for parts” were place around the plant and “Cheat Sheets” were printed and laminated on 3 x 5 cards.
Storeroom Operation
We’ve covered what information we should keep (master data) and maintain.
We went over how the parts should be organized in the storeroom.
So what is next?
After getting these two right now it’s time to see what operations are taking place inside our storerooms.
The basic operations are:
- Parts issuing
- Parts Receiving
- Parts return
Let’s see what good looks in these processes.
1. Parts issuing (dispatch)
This process is how maintenance or other departments evaluate our storerooms. In other words “Is the part available when I need it?” Parts issue at the storeroom should be for emergency or scheduled break-in work orders. A part kitting process (explained in a later article) where parts are identified and reserved in advance is best practice.
We can have the best in class storeroom; however, if the process of obtaining the part is a journey, the storeroom is ineffective. The issuing or part dispatch process is influence by:
- Size of store
- Store organization
- Accuracy of your equipment part list or BOM’s
- Searching capabilities of the CMMS
- Knowledge of personnel
What good looks like is to have a store room in which it is organized properly, parts can be searched online in a catalogue or CMMS, and all of this done in a 4 – 8 minute range for small parts and 20 – 30 minutes for large items.
2. Parts receiving
Receiving parts in the storeroom is not only about checking amounts received vs. amount ordered. What good looks in receiving should include:
- Visually inspecting part for condition and/or damage (box condition, parts wrapping)
- Checking parts catalogue number vs. purchase order information.
- Verifying stamped manufacturer and mfg. part number against part master data
- Verifying part location is appropriate.Examples:
- Large and heavy parts are placed on lower shelves
- Electronic boards being kept in their electrostatic bags and stored in an area free of airborne dust.
- Bearings stored properly
Best practice in receiving includes a quality inspection that includes verification of part specification, metallurgy, review of vendor certification sheets if required and others. It should include checking if needed to be part in a PM program
3. Parts return (after issued)
This process needs to be clearly identified. I have been in plants where stores are managed by purchasing and there is a storeroom policy that parts cannot be returned.
Usually, this policy comes after what I call a “let’s see if this one works” work habit of trades.
Parts will be removed from the store without any evaluation and/or investigation if it is the correct part. This has to be corrected at all levels from trades to supervisors.
What good looks like is a parts return process in place with the amount of transactions is a minimum.
This will reduce your annual inventory $$ spent, improve the company cash flow and reduce the storage cost.
As we continue it’s important to notice that ALL areas are important to obtain a storeroom that will provide the parts needed at the lowest inventory cost possible with quality and low premature failure.
Next up is Inventory Control.
In most places, Inventory Control is usually controlling the entrance to the store with a padlock and chain or a card reader. And yes, controlling the amount of persons entering the storeroom is important, much as other areas.
In materials management, inventory control consists of guaranteeing that a part identified as available in the storeroom is:
- Present
- Properly identified
- In the correct bin location
- In good condition (not used or broken)
- Clean, free of dust
- Stored in the proper environment
- Not defective, substandard or malfunctioning
- Complies with all specifications
In addition, Inventory Control deals with inventory levels (max, min, re-order point, requisitions). These will be discussed at another point.
Physical security of the storerooms
Access to the stores spare parts area needs to be controlled. When store attendants are present, they should decide who has access to the storeroom.
Typically, maintenance planners, supervisors and schedulers should have complete access to the storeroom. Trades access should be as needed and allowed by store attendant.
For unattended shifts, establish a process defining who has access and how to remove parts. This can be as simple as being escorted by security, area supervisor or group leader and writing down what was removed in a log.
Or it can have access control using cards and barcode scanner. Both need to have a well-documented process, people trained, and many BIG signs indicating the process.
The key for success is training and DICIPLINE.
In some locations, the store has “free issue” areas that consisted of nuts and bolts, rags and others. These areas should be separated from the main store.
I have seen storerooms with an Inventory Record Accuracy (IRA) of 98.5% in a 15K item numbers inventory.
How was that accomplished?
The process was documented, the maintenance and lead operators were trained, signs were placed all around the shop as a reminder of the process of removing a part, and two cameras were installed.
Inventory Record Accuracy (IRA) aka Cycle Count
The term cycle count refers to an accounting procedure. This procedure verifies that the amount of parts indicated in the CMMS equals the amount on hand.
IDCON INC uses the term Inventory Record Accuracy (IRA). Our method involves a reliability approach for this accounting procedure. Inventory Record Accuracy:
- Quantity accuracy
- Is the part in the correct location?
- Is the bin labeled?
- Is there a label on the part?
- What is the part condition?
- Complete (not missing components)
- New or rebuild
- Physical condition
If ALL conditions are met, the record is accurate.
When a person looks up a part in a CMMS or parts catalogue, and it is available (>0), the IRA method gives that person the assurance that the amount of parts indicated is correct, parts are identified, in a specific bin and ready to use. In short there are no surprises.
What to count and when?
Internal company procedures focus on and count the highest price items. This accounts for the items that represent 80% of the total inventory cost. Usually, high cost items are well known and when used, everybody knows it. In another words, the cycle count on these items hit 100% or very close.
IDCON recommends that you first identify all items using their current part usage as a guide. Parts can be:
Fast movers – Parts that have been issued during the last 6 months (< 6mo): These parts usually have a low purchase price and are used in many areas around the plant. They are usually 10% of the parts. IDCON recommends counting them 100% 3 times per year.
Slow movers – Parts that have been issued greater than 6 months and less than 2 years (>6mo and <2yrs): These parts are usually power transmission parts (bearings, seals, etc.) and are part of fixed time maintenance or a condition maintenance inspection. 100% 2 times per year
Very slow movers or non-movers – Parts that have never been used or not issued for the last 2 years: These parts are usually high price tickets such as transmissions, large HP motors, agitators, desiccant wheels, etc. They can be recently added for new equipment in the plant. 100% once per year.
The time frame of each category can be calibrated according to plant requirements. A spreadsheet using some macros can help you keep track of the counts.
Notice that a slow or very slow mover part can become a fast mover with just one transaction. This method frequently counts what’s being used and keeps tab on other items.
Has this been helpful?
If you’ll take this information and put it into practice, you will see changes.
But if you need help with your Materials and Spare Parts Management:
Feel free to contact us at [email protected] or join us for our next Materials and Spare Parts Open Training Course.