A while ago I was at a plant that had a set of vacuum pumps with a life of less than 3 months. I think most of us would say that is not normal, even if we are not vacuum pump experts. The process engineer was under the impression that the vacuum system needed to be redesigned.
An informal Root Cause Problem Elimination (RCPE) was initiated by the maintenance engineer and an experienced mechanic. They looked at the pump and the following observations were made:
• High vibration level
• Loosing vacuum on a regular basis
• City water make-up valve fully open
• V-belts slipping
• Bearings are running hot
• Heavy foaming from the seal water loop
• All parts heavily corroded
So what is there to do?
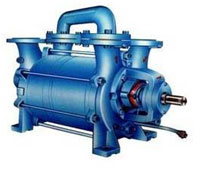
As smart maintenance people they started to look at each symptom. Their thought process was in terms of cause and effect based on their RCPE training. They carefully dismantled the pump and examined each part of the vacuum pump. In the first step they reviewed and corrected basic care like:
• Alignment
• Lubrication
• Cleaning of the cooler
• Balance the impeller
This made some improvement but not as much as expected. The challenge was still to find what was wrong with these vacuum pumps. The effort to improve took more than six months before they could find and correct all issues. The following list describes all the issue corrected:
• Too much overhung of sheave – bending shaft
• Wrong shaft material using 300 type vs. 400 SS – bending shaft
• Wrong clearance, shaft vs. impeller – loose impeller and key
• Seal water temperature too high – cooler fouled
• Wrong clearance between impeller and wall – losing vacuum
• Unbalanced impeller – high vibration
• Carbon steel parts used with caustic/nitric acid – corrosion
• Product leakage into vacuum system – holes in process filter
• Belt drive not aligned – vibration and wear
• Bearing housing fit too tight – too small clearance in bearings
• Bearing seals not made for water – water entering bearings during area cleaning
• Seal water heat exchanger too small for application – design
• Pump not assembled on flat surface – rebuild table missing
• Pump not aligned during installation – soft foot bending shaft
The life of these pumps is now 3 years instead of less than 3 months. The success of this informal RCPE is due to smart people in the organization and letting them spend time for problem solving. Well trained and SMART maintenance crafts and engineers are part of the foundation to build a good reliability and maintenance process in your plant.
Learning’s, what are the benefits of SMART employees in the organization?
• Cost is decreasing
• Free up resources
• Operations output is increasing