An obvious resource is to use for early detection of problems is training your operator in basic inspection techniques. You may have heard of the terms TPM or Autonomous Maintenance, in reality it’s all about engaging your operators in caring and inspecting equipment.
Who can better detect problems? They should be in tune with subtle changes.
Think about your car; with the exception of scheduled maintenance, the driver initiates 98% of shop visits. Most drivers also understand that finding problems early equals major savings.
The industry is well aware of the impact of preventive maintenance regardless if an operator or an hourly maintenance person performs it.
With downward cost and price pressure and aging equipment, many plants can barely keep fixing what breaks let alone perform simple equipment inspections with overtime-maxed maintenance people. The solution is clear. Break the vicious circle of reactive maintenance.
When recommending the concept of operator inspections, a wall of objections and obstacles might arise. Unions may claim this will eliminate work for their maintenance members although operators will be doing nothing more than inspections and what many union agreements already allow.
Another common objection from maintenance people, management personnel, and operators is that operators do not know how to do this.
The tasks operators should perform are simple, common sense inspections. Many operators can do such inspections without training. The fact that many operators maintain their vehicles and home means they are clearly capable of learning and performing complex maintenance tasks.
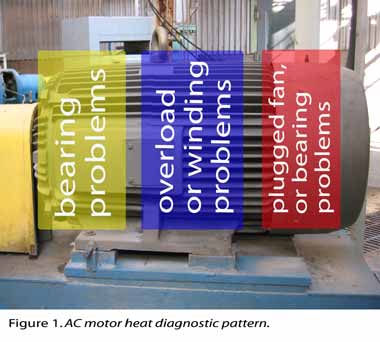
For example, ask an operator to inspect the AC motors in his area according to pre-set frequency and order as Fig. 1 shows.
If the temperature is high near the front, a bearing or alignment problem probably exists. If the temperature is high in the middle, the problem is undoubtedly a winding problem or overload. If the temperature is high at the back, airflow or bearing problems may exist.
I bet an operator can do this inspection!
Many operators are already recording operating parameters such as temperature and pressure. Typically, they file these.
Perhaps, a supervisor may examine them another day. This is often mere “busy work.” Teaching the “recorder” to interpret what he sees and then initiate action will provide many valuable front line observations, save uptime, and direct maintenance to the “hotspots” before they turn catastrophic.
Marking gauges with the normal operating range and using graphical, eighth-grade level instructions showing the “recorder” why, what, and how to inspect makes the job of an operator more interesting and truly empowers them to impact plant performance.
I bet an operator can do this!
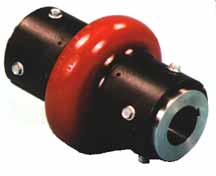
Most plants have couplings of the “tire” type, see Fig. 2. A simple inspection of a “tire” coupling is to visually inspect it for lose bolts, tears in the tire material, and worn keyways.
I bet an operator can do this
Managers need to decide if operator inspections are the proper action. If so, do not allow attitudes and objections to stand in the way. Forge ahead, make the plans, use pictorial training and reference material, send the Operators to Essential Care and Inspection Techniques Training, and institute the procedures.
This will definitely be a win-win situation for the operators, maintenance personnel, and the plant. I bet you can do this!
Our Condition Monitoring Standards are a great resource to train your operations team in inspection basics, they are available for you to purchase.
Download IDCON’s practical guide to implementing operator based reliability.
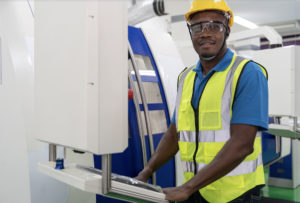