In the latest article I mentioned several areas that have to be improved for an organization to become lean. The focus in”lean thinking” is to reduce or eliminate losses.
In this column I like to discuss what I call “Lean Shut Down Management.”
Depending on the industry a shut down can be different in scale, for example:
- Several weeks for a stop in an oil refinery.
- Days for a longer shut down in a chemical plant.
- Hours for a recurring shut down in many process industries.
- Minutes for adjustments and tool changes in manufacturing industries.
- Seconds for a Formula 1 or NASCAR pit stop.
NASCAR is a good example of what can be accomplished through precision planning and scheduling and execution.
Major contributors to their pit stop, or shut down performance, include operations and maintenance communication and continuously working on improving the basics of Planning and Scheduling, Execution and Root Cause Problem Elimination.
In the nineteen fifty’s a good pit stop lasted around 240 seconds. If nothing had been done because everyone thought this is very good, then we would still have four minutes pit stops, but the crew that could bring it down to where it is today, at a record 12,6 seconds, would win the race.
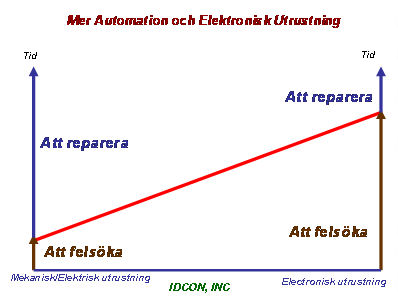
The driver of the car is in constant contact with the pit stop crew, they do not show up suddenly telling the pit crew “I think I have a problem with the right front tire” and the crew answers “We will go to the store and check if we have any replacement tire”.
But this happens daily in most plants. In a NASCAR race there is a strong motivation to win the race, in a plant there might be completely other factors driving motivation.
In addition to driving Planning and Scheduling to precision and excellence NASCAR pit crews are continuously working on improving the basics. This includes;
- Lug nut tool is turning at 24000 rpm.
- All parts sorted and placed on where they are used.
- Steering wheel straight position is marked.
- Wheel bolts rounded tops.
- Wheel nuts glued to wheel.
- IR measurement of tire temperature.
- Measurement of tire wear.
- Marked wheel position to speed up wheel change.
- Wheel nuts painted yellow for visibility.
- Analysis of problems and successes.
- Training 20 hours per week for 20 seconds of work on Sunday.
- Always do work right before fast.
Regardless of the length of the shut down, the same principles apply to make the shut down more effective or what we like to call lean.
- First and foremost we should produce without any problems between scheduled shut downs. Mean Time Between Production Losses (MTBPL) including Quality, Time and Speed) should be as long as possible.
- When we have a shut down we want to perform it with the right quality on all of the jobs and as quickly as possible.
The combination of how many shut downs you have and how long they are affects your production volume and your ability to deliver products on time.
It is a given that the shut down must be scheduled (when and who executes what) and that all the jobs must be planned (what, how, all the tools, spare parts and materials, lock out tag out etc. identified) before the shut down begins.
All shut downs should also have a time for freezing the schedule. After the freezing point in time no new jobs will be accepted without harsh criticism. Two measurements can be used to challenge your organization and to measure and show improvements.
- Number of added on jobs and changed jobs.
Define a scheduled shut down as a scheduled shut down if it is done within the agreed upon time-frame.
For example, 44 hours before a shut down for an eight hour shut down on a larger process line, four weeks before for a three week long shut down in an oil refinery and four hours for tool changes that has been scheduled to take approximately forty minutes.
Then measure how many jobs that are added or changed after the freezing point in time and during the shut down. Scrutinize all the added or changed jobs at latest, three days after the shut down. Have them explained and learn how they can be avoided next time you have a shut down.
- The relationship between scheduled and unscheduled shut downs.
With the same definition as in the previous paragraph, we can measure the relationship between scheduled and unscheduled shut downs.
For many process industries the quota of the equation is over 1 and should steadily increase.
This is on the condition that scheduled shut downs are not programmed and based on old habits but based on market and condition monitoring of process and equipment.
Do all jobs need to be done during a shut down?
It is not at all unusual that many of the jobs that are performed during a Shut down are only done because they have always been done and no one has ever questioned if they actually need to be done or not.
To know if what you are doing is right you must have a good understanding of the expected life for each respective component.
To, for example, regularly change a roller bearing after 8000 – 10000 hours of operation time cannot be right. Still, it is a common preventive recommendation from manufacturers.
Recently I discussed the recommendation to change the bearing of a centrifuge once per year. “The centrifuge rotates with a high r.p.m. and if a bearing breaks the rotating unit can cause severe damage, including bodily injury,” was the answer.
According to the bearing manufacturers’ calculations the life for a bearing is between 1 to 15 years. (L10 – L90 life span) It is calculated that ten percent break before one year of operation and ten percent are calculated to last longer than 15 years, in this application.
It is just that fact that indicates that it is wrong to change the bearings once per year. The bearing that is changed could potentially last for more than ten years whereas the new bearings might not last more than three years. Moreover you are always risking that a problem will be induced when you change a component.
Within reliability theory bearing failures are defined as random failures, you don’t know when failures will occur.
So that means you can’t know when it needs to be changed either. ”Even though I know that it isn’t right to change the bearings, I still do it,” the maintenance manager said to me. ”What do you think would happen if I didn’t change the bearings one year because I mounted a vibration sensor in the bearings and then measured the condition continuously, so I know when the bearings should be changed and we had a breakdown?”
He continued. ”I can always try to explain to the plant manager, who is an economist, that based on reliability theory it isn’t right to change the bearings once a year, it would instead be correct to base the change on the bearings’ condition.”
”We have, through the years, had several breakdowns, but we always came away without all too harsh words, if we had changed the bearings according to our existing preventive maintenance plan.”
The maintenance manager ended with, ”So it isn’t always that easy to become lean even if our plant manager pushes lean manufacturing hard.”
You should also always ask if the jobs that are done during the shut down could be done during production. One good example of innovation and new thinking is to change the joints electric power high voltage lines.
With the help of a helicopter and dynamite the old joints are improved without disruptions in power supply.